👷🏼 LRP
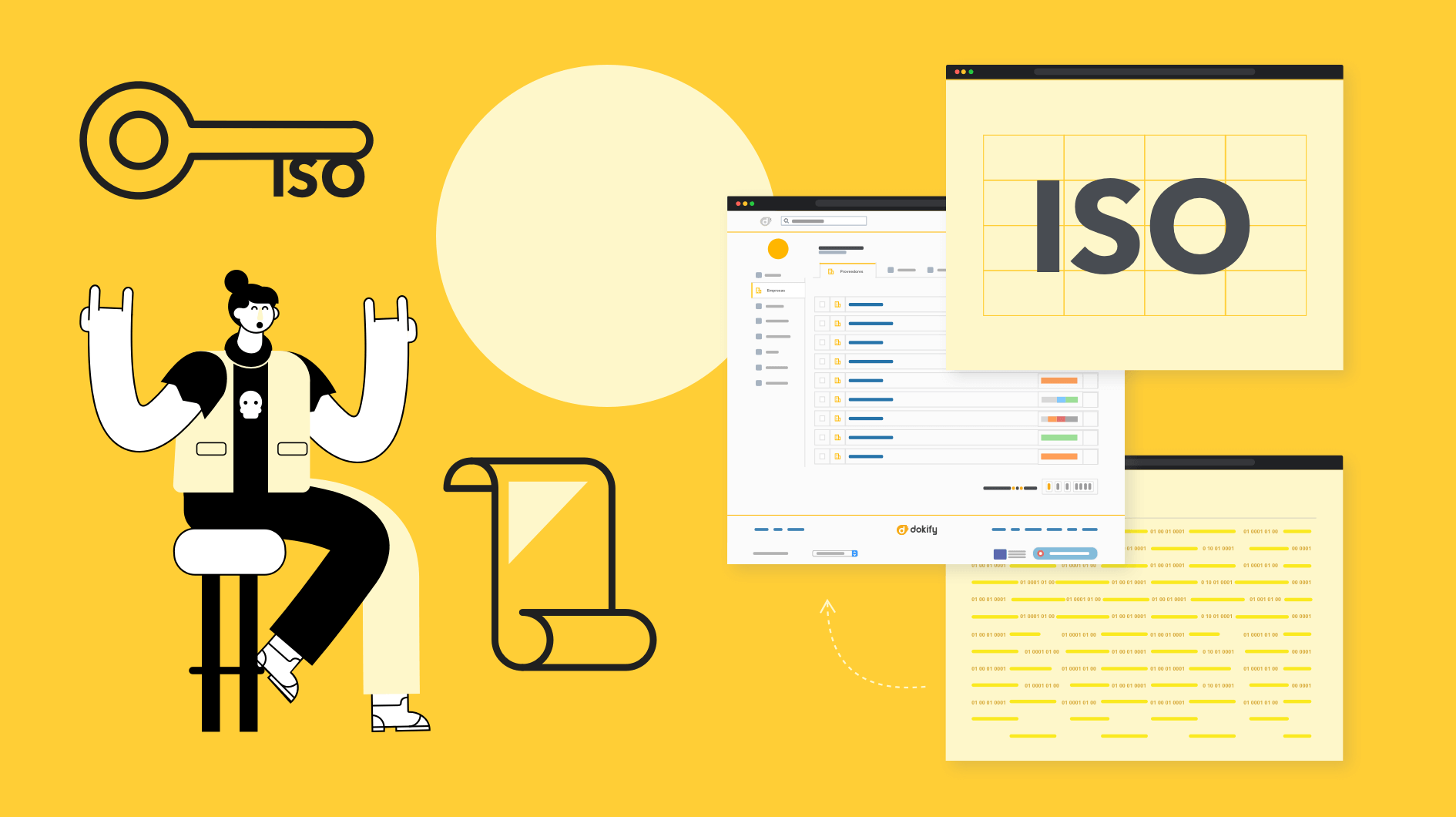
March 19, 2025
- x Min of reading.
Guidance on ISO standards and Supplier Approval
Do you know what the most important ISO certifications are? Does my company have to comply? Find out.
According to a press release issued by AENOR on 14 September 2020, the benchmark certification body in Spain, our country remains among the top ten in the world in the classification of the twelve main certifications and has risen in the ranking in most of them. This is revealed in the report of the International Organisation for Standardisation (ISO), corresponding to the 2019 financial year.
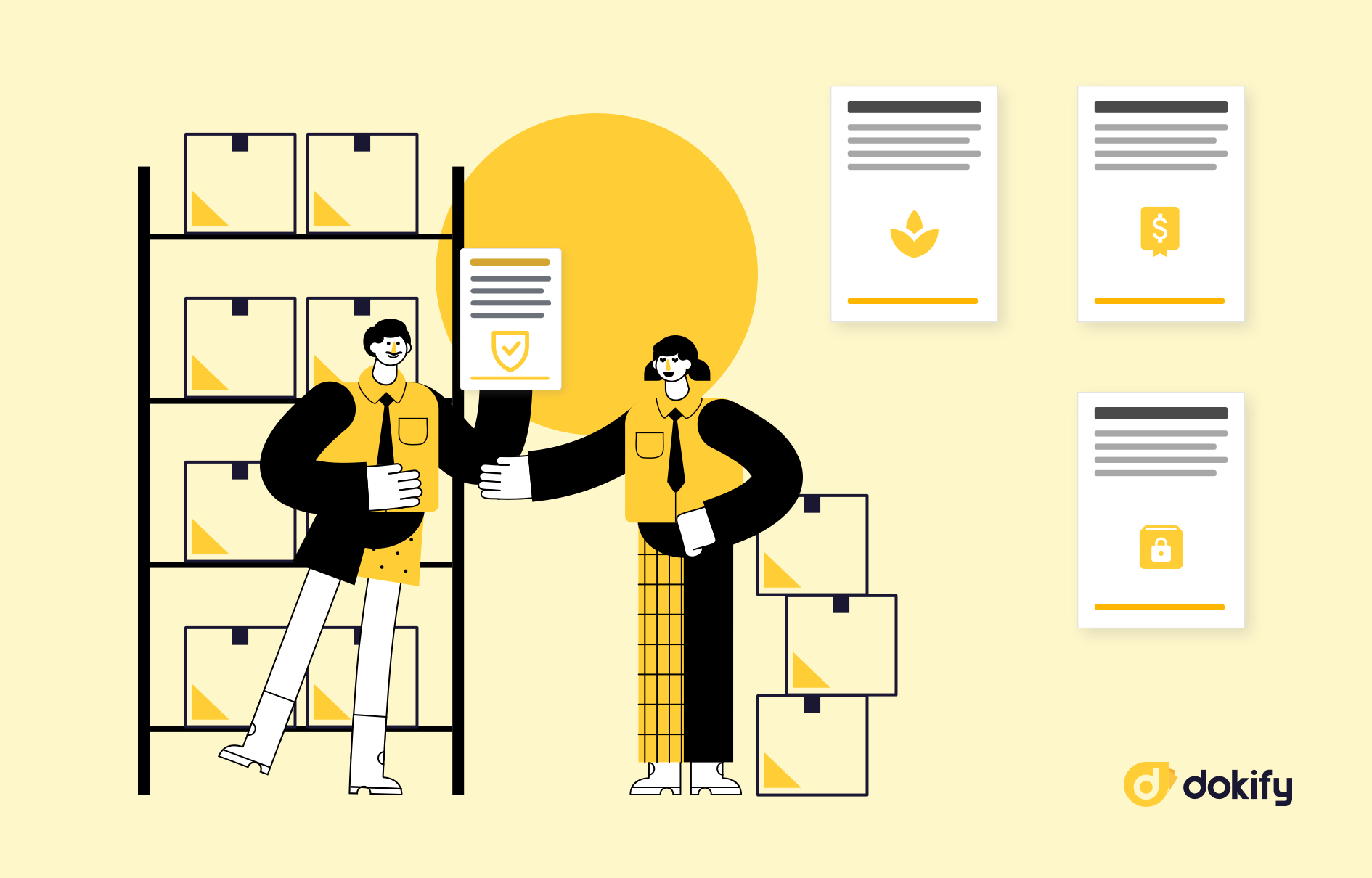
What are ISO standards?
ISO is a global network that identifies which international standards are required by business, governments and society, develops them together with the sectors that will use them, adopts them through procedures based on national multi-stakeholder input and offers them for global use.
ISO standards are based on an international consensus drawn from the broadest base of stakeholder groups. Expert input comes from those closest to the needs of standards and the results of their implementation. Thus, although voluntary, ISO standards are widely respected and accepted internationally by public and private sectors.
ISO, a non-governmental organisation, is a federation of national standards bodies from all regions of the world; one per country, including developed and developing countries, and countries with economies in transition.
Each ISO member is the main standardisation body in its country. In Spain it is AENOR. The members propose new standards, participate in their development and provide support, together with the ISO General Secretariat, to the 3000 technical groups currently developing the standards.
The 2019 ISO report reflects an overall increase of 3.8% compared to 2018.
In 2019, almost 2 million centres were certified worldwide and 100,000 in Spain, which shows that companies and institutions see certification as an effective tool for improving their competitiveness, which contributes to generating trust.
What are the most important certifications?
The most widespread certifications are Quality Management ISO 9001, Environmental Management ISO 14001 and Occupational Health and Safety ISO 45001. They do not expressly use the word supplier approval, but they do mention the need to know the supplier, their ability to meet the requirements of the system and therefore their prior evaluation and qualification, the application of contractor selection criteria in the purchasing processes and the obligation to keep documentary information, which in short is nothing more than what we professionals in the purchasing function call supplier approval.
Another issue is whether the approval procedures we have established in our companies adequately cover the requirements of the standards in order to be able to be certified in any of the aforementioned standards or, if we already have the certification, to be able to maintain it.
Does my company have to comply with the regulations?
Why is it "good" to comply with all these regulatory requirements?
Why is it the only way for my company to be certified in any of these Standards and thus be able to be approved to offer services or products to certain clients?
Or because my company is already certified and if the Purchasing or Quality area does not take care of these requirements regarding suppliers, my company may lose the certification and I will be blamed?
If those are the reasons why you are reading this article, don't go any further. Really, it's not worth your time. It's not worth your time.
If the organisation to which we belong decides to implement any of the 3 management systems mentioned above, it is, or should be, because its employees are truly convinced that it is going to:
- Improve your processes and eliminate the costs of 'non-quality', contributing to continuous improvement.
- To prevent occupational hazards to organisations and therefore accidents to their workers.
- Prevent environmental impacts and actually use the necessary means to avoid, reduce or control them.
If, in addition to all of the above, this "sells" to shareholders, customers and society in general, fantastic, but it should never be the first objective but a pleasant consequence.
According to a survey conducted on 14 April 2020 by the International Association for Commercial and Contract Management, 78% of responding members reported that, due to COVID, they had experienced disruptions and other problems in their supply chains.
Considering that in some sectors suppliers account for 40-60% of sales, securing sources of supply is key to being able to serve our customers.
Many suppliers have disappeared. Raw materials are scarce or simply not available. Price has taken second or third place. Nowadays, more than price, what is sought after is the guarantee of supply and this can only be achieved with a good approval methodology that allows the right supplier to be available at the right time.
ISO standards in the near future
The supplier market is constantly evolving, constantly changing and the pandemic has accelerated its pace of evolution.
There are suppliers who have had to change a lot so that nothing changes in the relationship with their customers, i.e. they have had to adapt quickly to the new situation in order to maintain their delivery commitments, accommodate order cancellations, unexpected increases...
The buying market is rewarding this adaptability of its suppliers, their flexibility, commitment and sometimes even creativity.
The proximity of supply sources and suppliers who inform us and anticipate risk situations are becoming more highly valued. Those who have protocols and contingency plans in place to avoid production stoppages.
In short, as I said, we have realised that we depend on our suppliers much more than we thought. There are many more supplier markets than we think within our borders.
And approval systems need to be more agile and add value by enhancing sourcing.
Supplier certification must cease to be the unfinished business of purchasing departments and become a strategic function.
3 reasons why you need a supplier certification tool