👷🏼 LRP
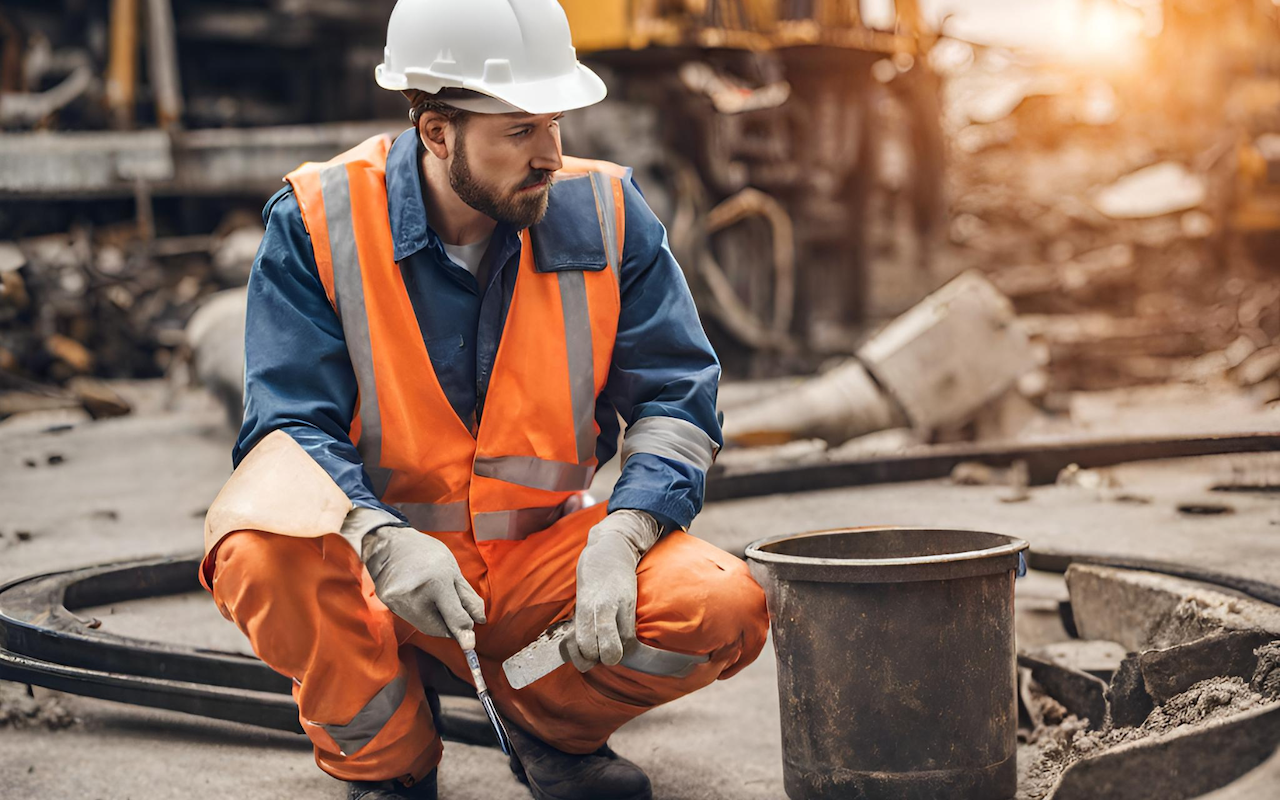
March 19, 2025
March 5, 2024
- x Min of reading.
Occupational safety inspection after an occupational accident
The occupational safety inspection detects causes and possible solutions, but for it to be effective, it is important to coordinate.
Following an accident in a workplace, it is essential to carry out an investigation. The occupational safety inspection detects causes and possible solutions, but for it to be effective, it is important that everyone involved understands its scope.
This is the inspection process after a work accident
We can divide an occupational safety inspection after an accident into six different stages, all of which are essential to determine the causes according to the Occupational Risk Prevention Law.
Preliminary considerations
Before beginning the inspection, it is crucial to make a number of preliminary considerations. This includes gathering initial information about the accident, such as the time, location, those involved and the nature of the incident. It is also important to establish the objectives of the inspection, which usually focus on understanding how and why the accident occurred.
The site visit should be planned, ensuring safe access and adherence to company protocols and health and safety regulations. This preparatory phase is essential to ensure that the inspection is thorough and effective.
Participants in the occupational accident
Identifying and understanding the roles of all parties involved is critical. This includes the injured person, witnesses, supervisors, co-workers and anyone else who may have relevant information about the accident.
Each of these responders can provide different perspectives on what happened, contributing to a complete understanding of the incident. In addition, identifying the responders helps to establish who will be interviewed and in what order.
Ocular inspection by labor inspector
The ocular inspection is a critical step, where the labor inspector examines the accident site. This process includes identifying any factors that may have contributed to the incident, such as unsafe working conditions, equipment failures or deficiencies in safety measures. The inspector will document everything meticulously, using photographs, notes and, if possible, collecting physical evidence.
This stage is essential to obtain an accurate picture of the working conditions at the time of the accident.
Description of the accident and determination of the causes
This phase involves reconstructing the events leading up to the accident, based on the evidence gathered and testimony. The goal is to create a clear and accurate narrative of how and why the accident occurred, including identifying immediate causes, such as human error or equipment failure, and underlying causes, such as deficiencies in safety processes or employee training.
Interviews with stakeholders
Interviews are essential to obtain direct information from those involved in and witnessing the accident. During this stage, the inspector should ask open and specific questions to understand the perspective of each party involved, maintaining a neutral and empathetic attitude.
Interviews should be confidential, to ensure that responders feel comfortable sharing information. The information gathered in this phase is vital to corroborate the details of the accident and to understand the antecedent factors.
Documentary analysis of the occupational accident
Documentary analysis involves reviewing all documentation related to the accident, including incident reports, training and maintenance records, and company safety policies. This review helps determine if proper procedures have been followed and if there are any deficiencies in safety management systems.
This analysis can also reveal whether the incident was an isolated event or part of a trend of similar incidents, which is crucial for implementing effective preventive measures.
Documentary analysis complements the information gathered in the previous phases and is essential to complete the final inspection report.
The Importance of Occupational Risk Prevention
Occupational Risk Prevention is crucial to avoid accidents and ensure the safety and health of workers in the work environment. By identifying and evaluating potential risks, companies can implement preventive and corrective measures to minimize or eliminate hazards, which not only protects the physical and mental integrity of employees, but also improves productivity and morale in the workplace.
In addition, prevention reduces costs associated with accidents and occupational illnesses, and ensures compliance with current legislation, avoiding penalties and improving the corporate image. By means of the Risk Assessment tool, it is possible to centralize the above information in a single digital space.
Documents required for an ORP inspection
Before an Occupational Risk Prevention (ORP) inspection, it is necessary to present the following documents:
- Risk assessment: Document that identifies the risks associated with each job and the preventive measures applied.
- Occupational risk prevention plan: The basic document detailing the company's prevention policy.
- Emergency and evacuation plan: Instructions and procedures in case of emergency.
- Employee training and awareness records: Proof of OHS training received by employees.
- Report of occupational accidents and occupational diseases: Record of incidents and corrective actions taken.
- Certificates of revision and maintenance of equipment and machinery: Documentation that verifies the good condition and safety of the equipment.
- Appointment of the person in charge of health and safety: Details of the designated technician or prevention service.
Infringements and penalties resulting from OHS inspections
Infringements arising from the Occupational Risk Prevention (ORP) inspection can be classified as minor, serious and very serious, depending on the nature and seriousness of the non-compliance.
Financial penalties vary according to the classification of the infraction and can range from moderate fines to significant amounts.
Minor infractions may include minor failures in documentation or out-of-date training of workers, while serious infractions may be the lack of adequate risk assessments or failure to provide the necessary personal protective equipment.
Very serious violations include exposing workers to severe risks without protective measures, or failing to report occupational accidents.
Sanctions not only involve financial penalties, but can also entail the suspension of activities, administrative sanctions or even criminal liability in cases of extreme negligence.