⚠️ Risk Assessment.
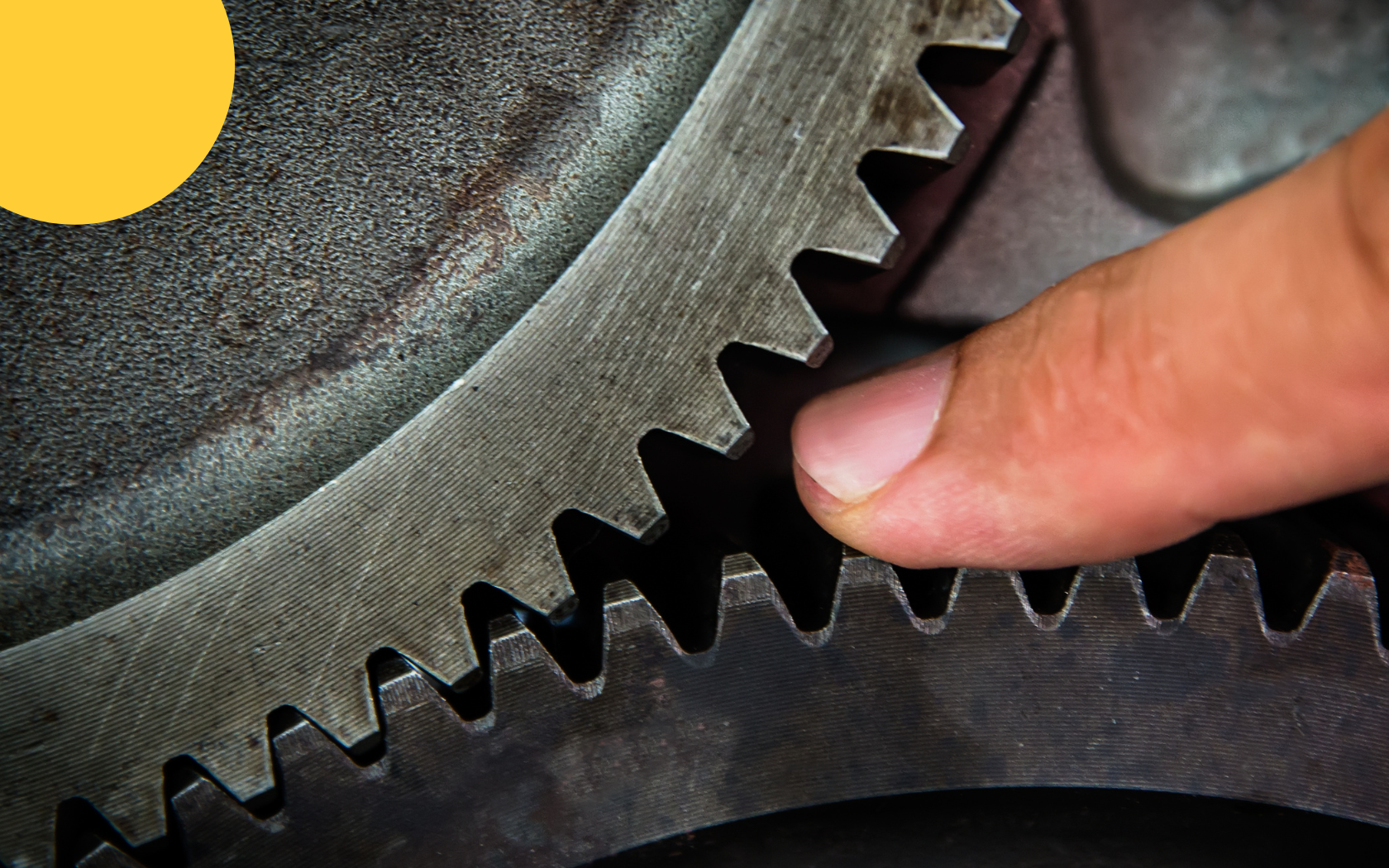
March 19, 2025
February 28, 2024
- x Min of reading.
How to make an occupational risk assessment?
The process for the correct evaluation of occupational hazards
Knowing how to carry out a risk assessment involves complying with a specific methodology, which makes it possible to identify and assess risks in the work environment.
Steps for Occupational Risk Assessment
The process for the correct evaluation of occupational risks consists of a series of stages, which result in the identification of risk situations.
Identify hazards by areas or sectors
The first stage of the occupational risk assessment is to identify the specific hazards present in each area or sector of the company, which involves a thorough analysis of the working conditions, processes, equipment and substances used. For example, hazards such as unguarded machinery, toxic chemicals, slippery surfaces or adverse weather conditions may be identified.
Identify the origin of the risks
Once hazards have been identified, it is important to determine their origin or cause; this process helps to understand why these hazards exist and how they can be effectively addressed. For example, the origin of a hazard may be the lack of training of employees in the operation of a hazardous machine or the lack of proper maintenance of equipment.
Identify those most affected
Each risk may affect different employees in the organization in different ways. It is critical to identify who is most affected or most at risk in each situation. The goal is to customize control measures and safety training to adequately protect workers.
Assessing risks
Risk assessment involves quantifying and rating the risks identified, it is important to consider the likelihood of an incident occurring and the severity of its potential consequences. The combination of these factors helps to determine the priority and urgency of each risk. This assessment allows an order of importance to be established in order to address the risks effectively.
Documenting findings
It is essential to document all findings of the risk assessment, including the list of hazards identified, their origins, the main parties affected and the results of the risk assessment. Documentation is crucial to keep an accurate record of the situation and provide a sound basis for decision making and implementation of control measures.
Establish an accident response plan
In the event of an accident, it is essential to have a response plan in place. This plan should include procedures for reporting, investigating and documenting the incident, as well as for providing medical care and support to those affected. It should also contain corrective and preventive measures to prevent similar incidents from reoccurring in the future.
Effective methods for risk assessment
Risk assessment is carried out at three different levels.
Qualitative method
This method is based on subjective descriptions of risks, categorizing their likelihood and severity in general terms, such as high, medium or low. It is useful for an initial assessment and for identifying notable risks, but does not provide a sufficient measure of risks.
Semi-qualitative method
It combines qualitative and quantitative aspects. Numerical values are assigned to the probability and severity of risks, allowing for a more accurate assessment without reaching the level of detail of a full quantitative analysis.
Quantitative method
It uses precise numerical data to measure the probability and consequences of risks. It relies on mathematical calculations and models to provide a more accurate estimate of the level of risk, which is especially valuable in complex and critical industrial environments.
What should be taken into account in the evaluation?
The most important criteria for determining how to conduct a risk assessment are as follows.
Activity to be developed
The first criterion involves understanding the nature of the activity to be carried out. This includes identifying the specific tasks that workers will perform, as well as the processes, tools and materials used. This information is essential to identify potential hazards associated with the activity in question.
Job characteristics
The jobs involved in the activity must be analyzed in detail, evaluating responsibilities, exposure to risks, physical and mental workload, and any other aspect that may affect the safety and health of the workers in their jobs.
Workers required to fill these positions
Identifying the employees who will fill the jobs is essential, which includes considering their experience, skills, training and physical capabilities. Each worker may have different safety needs and requirements.
Possibility of a worker having special needs
It is important to recognize if any worker has special needs, such as physical disabilities or particular medical conditions. Additional measures should be taken to adapt the work environment and working conditions to these needs, ensuring their safety and well-being.
Work teams
Evaluating the equipment used in the activity is crucial. This process involves verifying their state of operation, maintenance, the availability of built-in safety measures and the training required for their safe use.
Workplace conditions
Examining the workplace itself is essential. To do so, factors such as lighting, ventilation, ergonomics, the presence of hazardous substances and any other aspect of the work environment that may influence the safety and health of workers must be evaluated.
Automates Risk Assessment
Automating risk assessment using specialized software is a very effective tool for organizations wishing to improve occupational safety management. These programs allow for efficient collection, analysis and documentation of data related to occupational hazards.
The main advantage lies in the reduction of manual workload, which minimizes errors and saves time. In addition, the software can perform more accurate quantitative and qualitative analyses, allowing for a more complete assessment and more effective prioritization of risks.
Other advantages include automatic generation of detailed reports, real-time monitoring of the status of control measures and easy access to information by employees.
Automating risk assessment through software improves efficiency, accuracy and transparency in occupational safety management, resulting in a safer and healthier working environment.